Navigating to Zero - May 31
06/01/23
Do Safety Management System Standards Indicate Safer Operations? is the title of a 2022 working paper by faculty from the Harvard Business School that focuses on the British OHSAS 18001 Occupational Health and Safety Management standard, which was the basis for the 2018 International Organization for Standardization (ISO) 45001 standard that replaced OHSAS 18001 in 2021. The authors offer two hypotheses:
- Establishments with superior occupational health and safety performance are more likely to become certified to the OHSAS 18001 Occupational Health and Safety Management System standard.
- Being certified to the OHSAS 18001 Occupational Health and Safety Management System standard will lead establishments to improve their occupational health and safety performance.
The paper finds that both of these hold true for American companies. On the first hypothesis, the authors report that organizations that adopt a certified safety management system (SMS) are typically well prepared for certification under the OHSAS standard. The findings on the second hypothesis are less intuitive, however: According to the authors, organizations that start with a more robust SMS see further incident reduction and more safety improvements after certification, even though OHSAS 18001 does not set quality performance goals and does not spell out incident reduction targets.
Any safety professional knows that the reason a strong SMS leads to more progress post-certification is the emphasis on continuous improvement – a constant effort to look for ways to be better and safer. And that is why we share our best practices, near misses, and knowledge at each safety meeting. Whether on a vessel, at the office, or on stage at the AWO Safety Committees’ Summer Meeting (August 16-17 in St. Louis!), what we strive for is not perfection, but rather continuous improvement.
We Can Be HEROes
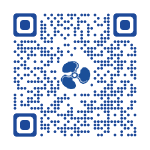
The American Waterways Honor & Excellence in Rescue Operations (HERO) Award recognizes rescues undertaken by AWO member company employees that demonstrate selflessness, skill, and bravery. AWO launched the program on March 1 of this year, recognizing our first awardees during the Safety Committees’ Winter Meeting. Since then, we have received several additional submissions, demonstrating the great things our mariners are doing every day to protect themselves, their crews, the environment, and the communities in which they operate.
Awardees receive a certificate for their vessel and a commemorative coin for each member of the crew involved in the rescue. Details about how to submit a nomination for the HERO Award and the submission form can be found on the AWO website. Please help us thank and shine a spotlight on our industry’s heroic mariners by sending in a nomination.
Congratulations to this recent recipient of the American Waterways HERO Award!
- Genesis Marine – Crew of the Sid Moller
Safety Professional's Corner
Joel Morton is a licensed deck officer with more than 20 years of experience in the marine industry. As Port Captain for Crowley Petroleum Services, Joel is passionate about helping employees work safely and efficiently, utilizing his years of experience and collaborating with others to find solutions for any situation.
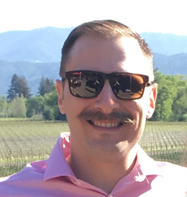
What are your safety program priorities for 2023?
Crowley has several ongoing safety programs. In my role in operations, I am focused on ensuring that these programs are understood and implemented on our vessels. I want to be sure the materials we present remain valuable as our company and our employees adapt to, and evolve with, new technologies, operations, and risks. Crowley is committed to continuous improvement in our safety programs and my priorities are in service of that commitment.
The first program I’ll highlight is “Safety in Motion,” which has been part of the Crowley safety portfolio for the past few years. The program specifically addresses soft tissue injuries, which can be common for workers who do repetitive motions or work with heavy tools. We work with the Safety in Motion program to develop best practices and optimize our processes to mitigate the risk of these types of injuries.
This year, we are focused on making the program easier to access on vessels, which presents a challenge as the materials are primarily disseminated online, and our vessels do not always have reliable access to the internet for streaming videos. Compounding this issue, the time during which a coastwise tug and barge crew does have strong internet reception is when they’re in port. This is also when the crew must be focused on navigation, taking on supplies, conducting audits and inspections, and transferring cargo.
We want our crews to be focused on safe operations while in port, so it became a priority to develop a way for our mariners to access the Safety in Motion program while underway outside of the congested port access routes. My colleague, Andrew Ghiglia, took on this challenge, working with the team at Safety in Motion to produce hard copies of the course materials. The hard copies allow the crew to access materials when it’s convenient for them, effectively reducing the chance of distracting them from safe port navigation and providing an opportunity for crews to focus on the content in a less busy environment and apply it to reduce potential injuries.
Another important program is the Fleet Safety Officers program, which is unique to Crowley. This program utilizes former Crowley Chief Engineers and Captains who travel across the fleet, visiting vessels, dry docks, and other locations to lead safety initiatives. Presently, there is a particular emphasis on safety during shipyard visits, as we have seen a trend of higher incident rates for our vessels in the shipyard. This could possibly be because the crew is working on an adjusted schedule, performing unfamiliar work, or interacting with a safety system that is unique to the shipyard they are visiting.
Additionally, Crowley noticed that crews on vessels in the yard became somewhat isolated from management as typical meetings between crews and management follow operational routines, which are disrupted when the vessel is temporarily taken out of service. To address this, we empower the Fleet Safety Officer, which in this case is called the “Shipyard Safety Officer,” to establish regular communication with crews in the yard and build a bridge between the vessel crew and shipyard crew. By doing this, we ensure effective communication and collaboration between the two parties, and we can be sure everyone in the shipyard fully understands our safety concerns and prioritizes the well-being of our crew.
Our focus on soft tissue injuries and crew engagement in shipyards is a natural progression of our safety program and evidence of the success of past safety initiatives. Crowley is pivoting from programs of the past that effectively reduced spill frequency and improved our licensing support programs and compliance training regimes, and now seeking continuous improvement by looking at the details of past incidents, focusing on the contributing factors, and developing initiatives to reduce residual risk and drive incident rates closer to zero.
Can you talk about Crowley’s safety culture and an example of how you promote culture across the organization?
Crowley’s safety culture centers on our belief that safety begins and ends with each employee. To promote this, we are focused this year on the implementation of a Human Organizational Performance (HOP) philosophy. HOP is a science-based approach to looking at mistakes that enables an organization to address the root causes of mistakes more effectively. The general concept is that it’s okay to make a mistake or an error, and the best way to address the error is through an investigation that identifies the system or process that failed, offering the opportunity for the company to design an engineering control or procedural revisions to prevent the mistake in the future.
The idea that a system or process, not a person, is the root cause of most incidents is familiar to safety professionals. I’ve personally seen it in training that I participated in during an ARMS Reliability program several years ago. One of the key takeaways from that training was, “people are very rarely the root cause.” HOP takes this idea a step further by focusing on how an organization may learn from mistakes and address the failures in a way that mitigates the impact of those failures if they are made in the future.
HOP requires a change in mindset regarding problem-solving, from deck level to the corporate office. To ensure we extract maximum value from the HOP philosophy we need to support the active participation of every individual at Crowley. To achieve this, we have established a HOP Task Force that includes Port Engineers, Port Captains, and crew members. This task force ensures that all levels of the company are engaged in the program. Regular training sessions are conducted approximately once a month to introduce and familiarize everyone within the company with the program. We understand that implementing this cultural shift will take time, but our goal is to ensure that everyone understands and embraces the program, which is key to achieving true buy-in.
The National Safety Council is an essential resource for this program, and we encourage everyone to explore it further to gain a deeper understanding.
You have been very successful in your maritime career! Can you share what you like about our industry and advice for someone who is considering maritime transportation as a career?
The maritime industry offers something much bigger than just a job. It’s similar to my experience growing up in the Scouts and playing sports, the feeling of being part of a team that is bigger than the individual players. Joining a vessel crew or assuming a management role in the maritime industry allows you to witness firsthand how your actions can directly impact others and contribute to a vital piece of the American supply chain and economy. We are the backbone of the nation's transportation infrastructure, and I take immense pride in that fact. Nearly everything we use in our daily lives, from shoes to furniture to gasoline, has passed through a port. This realization reinforces the importance of our work and provides a sense of purpose.
Another aspect I cherish is the remarkable opportunities the maritime industry provides. Even with just a high school diploma, if you possess a strong work ethic and show up, you can achieve levels of growth that may not be possible in many other industries. The potential for personal and professional development is astounding. That's why it is important for me to be involved with organizations like AWO, as it allows me to give back to the industry on a national stage. Through collaboration with the Safety Leadership Advisory Panel and the many meetings and knowledge sharing opportunities that AWO and other industry groups provide, we have the opportunity to improve and strengthen our industry and our nation's supply chain, making it safer and more efficient.
My advice to anyone considering maritime transportation as a career is simple: put yourself out there. It doesn't matter if you are experienced or just starting out; you have to be proactive and engage with the maritime community. Join local maritime clubs, participate in programs like Sea Scouts or consider attending a maritime school and seize every opportunity to meet and learn from others in the industry. For the longest time, I believed that I wasn't ready to participate because I lacked certain skills or titles, but I was mistaken. It is crucial to immerse yourself in the industry, as it will pay dividends not only in your service to the industry but also in your personal growth and future endeavors.
In summary, my advice is to show up, be ready to work, and continuously learn. By doing so, you can secure a great career that may seem unattainable in other industries. That is the message we strive to convey—where else can you go from having a high school diploma to becoming a licensed captain in just four years?
AWO High Potential Learning Value Near Miss
Near Miss and Stop Work events are leading indicators that provide operators with an opportunity to identify and address weaknesses in a safety management system, before a hazardous condition or lack of procedure contributes to an injury or incident.
We are highlighting recent High Potential Learning Value Near Misses submitted voluntarily by AWO members. To submit your own Near Miss or Stop Work event, please use this form.
What is a High Potential Learning Value Near Miss?
A High Potential Learning Value Near Miss or Stop Work event is one that potentially prevents an injury or incident by:
- Identifying a hazard in the workplace that could result in injury or incident; and
- Providing an opportunity for reflective learning that has broad application to other mariners or operations.
If the identified hazard is left uncontrolled, it has a medium to high probability of occurring.
Navigating Without Required Pilots
MEMBER-SUBMITTED NEAR MISS 23-02
A coastal tug was approaching a Florida seaport. With one hour to go until arriving at the pilot boarding area, the Second Mate notified the pilots, and they responded that the tug would be the number two inbound vessel following a ship that was approaching from the east. Soon after, the tug went to Watch Condition 2 with the Chief Mate and Second Mate in the wheelhouse.
As the tug neared the pilot boarding area, she slowed speed to give the ship plenty of space to make its approach and board its pilot. The Mates were reviewing the local Fleet Notice when the pilots contacted the tug on VHF 14. The pilots asked the tug to start inbound, following the ship, and said that they would board after the tug was inside the jetties. The Mates immediately disagreed with pilots, and the Chief Mate explained that their company policy required an offshore boarding by the pilots.
After this exchange, the pilot dispatch/boat operator admitted that the tug’s pilot was still driving in, stuck in traffic, and not on the pilot boat. After the pilot boarded the inbound ship, the pilot boat had to go back to the pilot station, get the tug’s pilot, then return to the pilot boarding area. Had the tug followed the initial directions of pilots, the unit would have transited 40 to 45 minutes into the seaport, past the jetties, without the required pilot onboard.
POSSIBLE IMPACT OF THIS EVENT COULD HAVE INCLUDED:
|
|
LESSON LEARNED & FUTURE RISK MITIGATION:
|
|
NTSB Releases Quarterly Summary of Marine Safety Events
The summary highlights key safety factors for each of the six included NTSB investigation reports. Of the six incidents, there were two bridge allisions, one offshore platform allision, one fire, one breakaway, and one loss of a crane on board a construction barge. The key safety factors to which each incident was attributable are listed below, and details of the incidents can be found on the NTSB’s website.
Incident
|
Key Safety Factor
|
Crew fatigue
|
|
Combustible materials and smoldering fires
|
|
Construction barge crawler crane movement
|
|
Impairment
|
|
Bollard inspections
|
|
Navigation assessments
|
Coast Guard Safety Alerts
The Coast Guard has issued a Marine Safety Alert urging vessel operators to review and comply with load line requirements. Safety Alert 06-23 from the Inspections and Compliance Directorate summarizes a recent marine casualty resulting in the total loss of a crane barge, estimated at over $6 million. The incident occurred approximately 18 miles offshore Louisiana in the Gulf of Mexico while the crane barge was being towed in calm weather conditions. The barge was uncertificated without a load line and the operator did not request a Single Voyage Load Line (SVLL) Exemption from any Coast Guard unit before transiting beyond the Boundary Line.
Over the course of the investigation, the Coast Guard discovered major modifications to the barge arrangement and other conditions which compromised its seaworthiness. This would have precluded issuance of an SVLL exemption until corrected. Additionally, prior to capsizing, the vessel made multiple voyages outside the Boundary Line without a load line, violating U.S. statutory requirements and placing the vessel and crew at risk.
As a reminder, whether inspected or not, most commercial vessels 79 feet and longer are required to have a load line when operating outside the Boundary Line. The Coast Guard strongly recommends that vessel owners and operators review vessel requirements for load lines as specified in 46 CFR Subchapter E, Parts 41 through 47, and further explained on the Coast Guard’s Load Line website and Load Line Policy Notes. Questions concerning load line requirements can be submitted to the Coast Guard’s Naval Architecture Division (CG-ENG-2) at HQS-SMB-CGENG@uscg.mil.
The Bureau of Safety and Environmental Enforcement (BSEE) Safety Alerts
BSEE Safety Alerts are used by BSEE to inform the offshore energy industry of circumstances surrounding an incident or a near miss. They also share recommendations that can help prevent the recurrence of such an incident on the OCS, and many of the lessons learned are applicable to marine operations everywhere.
BSSE Safety Alert No. 464, Unexpected H2S Detection at Offshore Facilities, discusses finding hydrogen sulfide gas (H2S) in unexpected locations. H2S is mostly associated with production from sour petroleum reservoirs; however, it can also form in low-oxygen environments due to microbial activity during the decomposition of organic material or microbial reduction of sulfates. As a result, H2S production may occur unexpectedly in areas such as bilges, storage tanks, ballast tanks, chemical totes, and out-of-service process equipment.
|
H2S Levels Impacting Personnel Safety
|
|
Immediately Dangerous to Life and Health (IDLH):
|
100 ppm
|
Permissible Exposure Limit (PEL):
|
20 ppm
|
Recommended Exposure Limit (REL):
|
10 ppm
|
Typical alarm set points for…
|
|
Stationary detectors:
|
20 ppm
|
Portable detectors
(handheld/wearable): |
10 ppm
|
H2S Safety Tips:
- Ensure personnel understand that H2S may be encountered in unexpected locations.
- Conduct periodic inspections of stagnant holding tanks to ensure no H2S is present.
- Perform drills focused on unexpected H2S encounters, even in operations that do not move petroleum.
- Stay upwind when opening tanks and utilize a multi-gas detector to survey for the presence of H2S.
- Always test voids and only allow trained personnel to enter them.
- Ensure the Job Safety Analysis includes a discussion of unexpected encounters of H2S and any mitigation necessary when conducting work in areas that have a higher threat of bacterial-generated H2S production (i.e., ballast tanks).
- Follow H2S guidelines per 30 CFR 250.490.
Subcommittee News
Tankering and Barge Operations Subcommittee
![]() |
The Tankering and Barge Operations Subcommittee presented on May 22 at the International Liquid Terminals Association (ILTA) International Operating Conference in Houston. Chair Josh Dixon of PSC Group and James Loughlin of Midwest Tankermen presented Gangway! Insightful Approaches to Marine and Dock Safety with Dan Somma of Marathon Petroleum and Nils Duurkoop of Verhoef Engineering to an audience of ILTA members.
The next meeting of the group will be held in person on August 16 in St. Louis. Sign up to join AWO for this meeting on your member dashboard.
Falls Overboard Subcommittee
AWO’s Falls Overboard Subcommittee is made up of carrier and affiliate members with an interest in developing real-world solutions to address falls overboard, the leading cause of fatalities in the barge and towing industry.
The Subcommittee met virtually on April 24 to review its draft report on the prevention of falls overboard and discuss standards, policies, tools, and equipment that may help mitigate the risk of falls from an unguarded edge of a barge. Plans are in place to hold virtual meetings in July to continue the review process in anticipation of the report’s presentation at the Safety Committees’ Summer Meeting in St. Louis. If you would like to participate in this subcommittee, please email safety@americanwaterways.com.
Distracted Operations Subcommittee
The Distracted Operations Subcommittee is working to identify sources of distraction and develop tools to mitigate the risk of distractions as a contributing factor in marine casualties. Through the subcommittee’s work, AWO has published a Sterile Wheelhouse Guide and a Deckhand Distracted Operations Guide. The Distracted Operations Subcommittee will meet in July to discuss the draft Guide to Mitigating Distracted Operations. If you would like to participate in this subcommittee, please email safety@americanwaterways.com.
Environmental Stewardship Working Group
AWO is working with members of the Environmental Stewardship Working Group to develop and publish an updated version of our Voluntary Environmental Stewardship Best Practices.
The diverse operational profiles of AWO’s members mean that there is no one-size-fits-all solution for companies looking to reduce their impact on the environment. The Voluntary Environmental Stewardship Best Practices do not create rigid rules; rather, they detail potential practices in a catalog that can serve as a resource for members beginning, or seeking to take the next steps on, their sustainability journey.
If you would like to be a part of the working group, please contact Leah Harnish.
SSRP – We Need Your Input!
The value of AWO’s Safety Statistics Reporting Program depends on the full participation of all eligible members. This includes carrier members who employ or are responsible for vessel crews in their operations. Please visit the Safety Statistics Reporting Program website and enter your data for the first quarter of 2023, as well as any historical data that may be missing. Your submission is confidential and crucial to our industry’s benchmarking, advocacy, and safety and sustainability initiatives. If you have any questions, please feel free to contact me at mbreslin@americanwaterways.com or (504) 417-2136.
Don’t forget to start making plans to join AWO’s Interregion and Coastal Safety Committees on August 16-17 in St. Louis for our Summer Meeting, which will showcase the work of the Falls Overboard Subcommittee and feature presentations on a new near miss reporting initiative from the Maritime Administration, sustainable marine engine technology from Caterpillar®, and much more.
Wear Your Life Jacket to Work Day
May 19 was “Wear Your Life Jacket to Work” Day. AWO’s Safety Leadership Advisory Panel members answered the call and shared images of themselves wearing their life jackets in the office, on boat visits, and even at home to increase awareness of the importance of ALWAYS wearing a life jacket when exposed to a risk of a fall to water.
![]() |
![]() |
The American Waterways Honor & Excellence in Rescue Operations (HERO) Award recognizes rescues undertaken by AWO member company employees that demonstrate selflessness, skill, and bravery. AWO launched the program on March 1 of this year, recognizing our first awardees during the Safety Committees’ Winter Meeting. Since then, we have received several additional submissions, demonstrating the great things our mariners are doing every day to protect themselves, their crews, the environment, and the communities in which they operate. |